UNA DE CAL Y OTRA DE ARENA. DEL REVOCO A LOS ESTUCOS.
Guarnecido, enlucido, enfoscado, monocapa, revoco, estuco… ¿Qué diferencia hay entre estos revestimientos? ¿Qué materiales se utilizan en su composición? Con este post intentamos arrojar un poco de luz sobre los distintos tipos de revestimientos continuos, centrándonos en los que tienen base de cal por sus propiedades en rehabilitación y restauración de edificios históricos.
La cal, el cemento y el yeso son los conglomerantes más utilizados como base en revestimientos continuos. Estos materiales proceden de distintos minerales y, por tanto, tienen diferente composición química:
- Cal: Procede de la calcinación de la roca caliza (carbonato cálcico)
- Cemento: Mezcla de caliza (carbonato cálcico) y arcilla (silicatos)
- Yeso: Procede del sulfato de calcio
Los morteros se obtienen añadiendo a los dos primeros agua y áridos en distinta proporción. Así, tenemos morteros de cal, morteros de cemento y morteros bastardos (cal y cemento). Los áridos utilizados, su granulometría y la proporción utilizada dan lugar a diferentes tipos de morteros con diferentes propiedades. El yeso, en cambio, se puede utilizar mezclado exclusivamente con agua.
Yesos y morteros se utilizan como revestimientos continuos en construcción. De esta manera, tenemos:
- Guarnecido: A base de yeso negro, su principal uso es como primera capa en paramentos interiores. Tiene un acabado menos fino que el enlucido.
- Enlucido: Es la capa de acabado de yeso blanco colocada sobre el guarnecido. Sobre el enlucido se suele pintar, aunque también se puede aplicar directamente un barniz consiguiendo de esta manera un aspecto más natural.
- Enfoscado: Es un revestimiento formado por una capa de mortero de cemento o de cal con árido fuerte y aplicado directamente sobre el muro. Normalmente se utiliza en cámaras y exteriores y se puede pintar directamente o utilizarse como base para un acabado posterior de revoco.
- Monocapa: De base cementosa y pigmentado en masa, se suele utilizar en exteriores como alternativa al enfoscado y pintado.
- Revoco: Consiste en la aplicación de mortero de cal o de cemento con una granulometría fina de árido sobre una base previa de enfoscado. Según el árido utilizado, las capas aplicadas y las herramientas usadas, se pueden obtener distintos acabados (madrileña, martillina, rasqueta, finjido…)
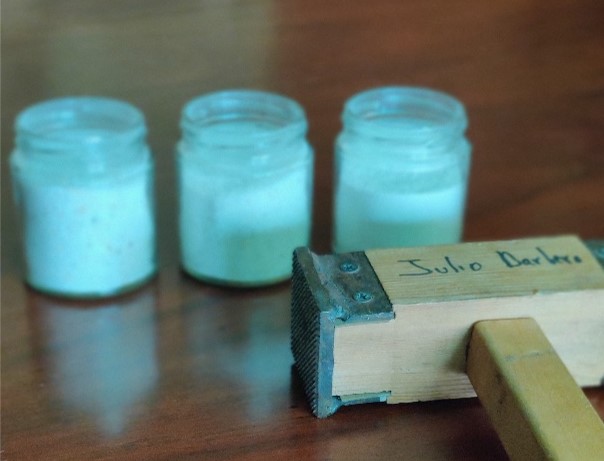
- Estuco: Se compone de mortero de cal, polvo fino de mármol y pigmentos. Se aplica en distintas capas (magra, repretar, enlucido, tinta…) sobre una base de revoco liso y permite un acabado muy fino y aspectos brillantes similares al mármol pulido. Existen distintos tipos de estucos, pero en España los más habituales son el estuco liso lavado y el estuco al fuego. Éste requiere unas primeras capas de liso con distintas granulometrías, 3 manos de tinta (agua de jabón y pintura de cal) y aplicación del hierro de estucado.
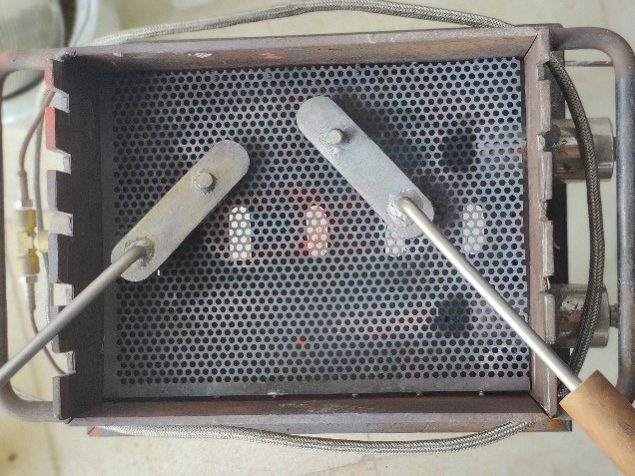
En Antana nos gusta la cal. Además de su intrínseco carácter reciclable (retorna a su composición natural con el paso del tiempo), sus propiedades físicas la hacen idónea en ciertas intervenciones de rehabilitación. Nos centramos en este post en los morteros a la cal y sus aplicaciones.
Proceso de fabricación de la cal aérea y cal hidráulica:
El proceso de fabricación de la cal y sus morteros es natural y sencillo:
- Se parte de piedra caliza (CaCO3) lo más pura posible (por encima del 95%). Las piedras se queman (calcinan) por encima de 900º y en este proceso se desprende CO2 y aparece óxido cálcico (CaO). En las piedras más gruesas el proceso de combustión no llegará al centro por lo que habrá que “pelarlas” y desechar el “hueso” (centro que se mantiene como caliza)
- El óxido cálcico (cal viva) es un producto muy cáustico que reacciona con el agua desprendiendo calor y produciendo hidróxido cálcico Ca(OH)2. A este proceso se le llama “apagado de la cal” o hidratación de la cal y se puede realizar por aspersión o por inmersión. El resultado del proceso por aspersión (cantidad mínima de agua) es el hidróxido de calcio en polvo. En cambio, el proceso por inmersión da lugar a la cal en pasta o cal grasa con más contenido de agua, lo que le aporta elasticidad y homogeneidad en el proceso de carbonatación que veremos más adelante. La cal grasa se mantiene con una capa de agua por encima para evitar que se inicie la carbonatación. Esta cal grasa puede reposar durante muchos años y, de hecho, el paso del tiempo mejora sus propiedades. Antiguamente, en ciertas zonas de España, cuando nacía un niño se apagaba cal por inmersión y se mantenía protegida con agua para utilizarla años después en la construcción de su casa.
- Esta cal se mezcla con áridos (normalmente, de mármol) y agua dando lugar a los morteros de cal. Reacciona con el aire (cal aérea) mediante un proceso de carbonatación absorbiendo CO2 y dando lugar, de nuevo, a carbonato cálcico (CaCO3). En este proceso el mortero va endureciéndose progresivamente, desde la zona en contacto con el aire hacia adentro, lo que le confiere su flexibilidad característica.
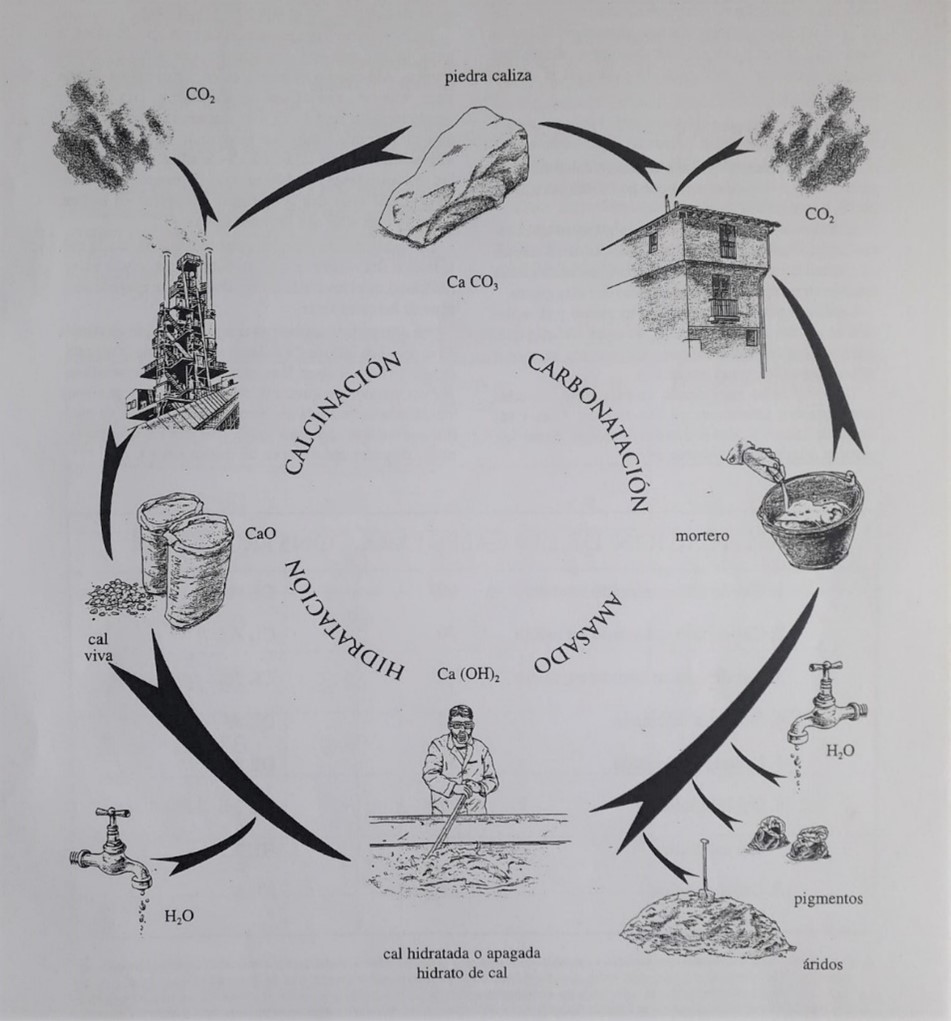
Las principales diferencias entre cal hidráulica y aérea son:
- Cal aérea: Procede de piedra caliza (CaCO3) con bajo porcentaje de impurezas. Una vez ha secado, endurece lentamente por carbonatación en contacto con el aire. No es recomendable su uso en ambientes húmedos o en intervenciones que requieran resistencia a corto plazo.
- Cal hidráulica: La cal hidráulica tiene menos cantidad de cal, bien por proceder de piedras menos puras, bien por la adición de otros productos (arcillas, puzolanas…). La cal hidráulica fragua primero por hidratación de las arcillas en contacto con el agua y después endurece por carbonatación de la cal en contacto con el aire. Esta doble reacción le confiere resistencia a corto plazo y posibilidad de trabajar en ambientes húmedos sin perder la plasticidad y flexibilidad de la cal aérea.
Ventajas de la cal
Las ventajas de la cal son múltiples:
- Sostenibilidad y reciclabilidad: En el proceso de calcinación no se superan los 1000º y, por tanto, no se produce mucho CO2. En cambio, en el proceso de carbonatación, la cal absorbe CO2 retornando a la composición original de piedra caliza. Este proceso y la ausencia de aditivos lo convierten en un material reciclable.
- Durabilidad: Los morteros de cal duran más que los de cemento. Éstos se deterioran rápido por diversos motivos, mientras que los morteros de cal bien fabricados y aplicados pueden durar siglos.
- Propiedades sanitarias: Al ser un producto cáustico evita la proliferación de microorganismos
- Facilidad de uso: Tiene baja retracción y buena adherencia. Es plástico y fácilmente manipulable, permitiendo un amplio abanico de texturas y cromatismos.
- Aislamiento: Al endurecer progresivamente, de fuera hacia dentro, es un material “estratificado”, con capas de distinta dureza, lo que le convierte en buen aislante térmico y acústico.
- Permeabilidad al vapor de agua: Es poroso, lo que permite “respirar” al edificio y evitar condensaciones.
- Compatibilidad: Los morteros de cal presentan bajas resistencias mecánicas, lo que los hace compatibles con distintos soportes y, por tanto, idóneos en rehabilitación y restauración de edificios históricos.
- Flexibilidad: El proceso de carbonatación de fuera hacia dentro lo convierten en un material flexible, capaz de absorber pequeños movimientos sin fisurar, evitando de esta manera la entrada de agua.
Usos de la cal
Los morteros de cal se utilizan mucho en todo tipo de obras pero, especialmente, en obras de rehabilitación y restauración de edificios históricos. Alguno de los usos de la cal en construcción:
- Revestimientos exteriores e interiores (revocos, estucos, pinturas…)
- Rejuntado de consolidación
- Rejuntados de piedra y ladrillo
- Colocación de tejas, ladrillo y piedra
- Regularización de paramentos
Desde Antana prescribimos el uso de la cal y la recuperación de la industria y artesanía derivadas de su fabricación y aplicación. Es un material reciclable, duradero, higiénico, transpirable, flexible y de fácil aplicación. Sus propiedades físicas lo hacen un material especialmente indicado en rehabilitación y restauración.
Este post ha sido redactado con la colaboración de Julio Barbero, empresa especializada en fabricación y aplicación de morteros de cal.
También te gustaría
Tendencias relacionadas
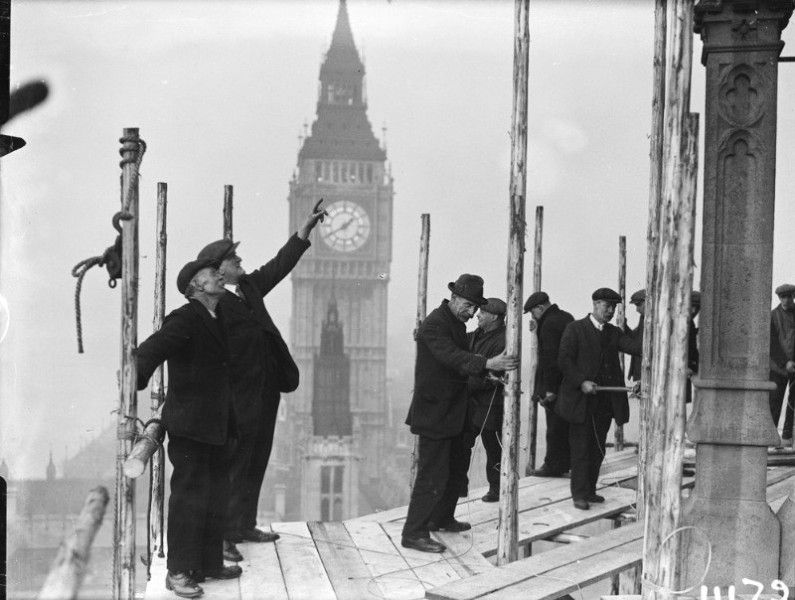
Construcción de edificios: Belleza en el tajo
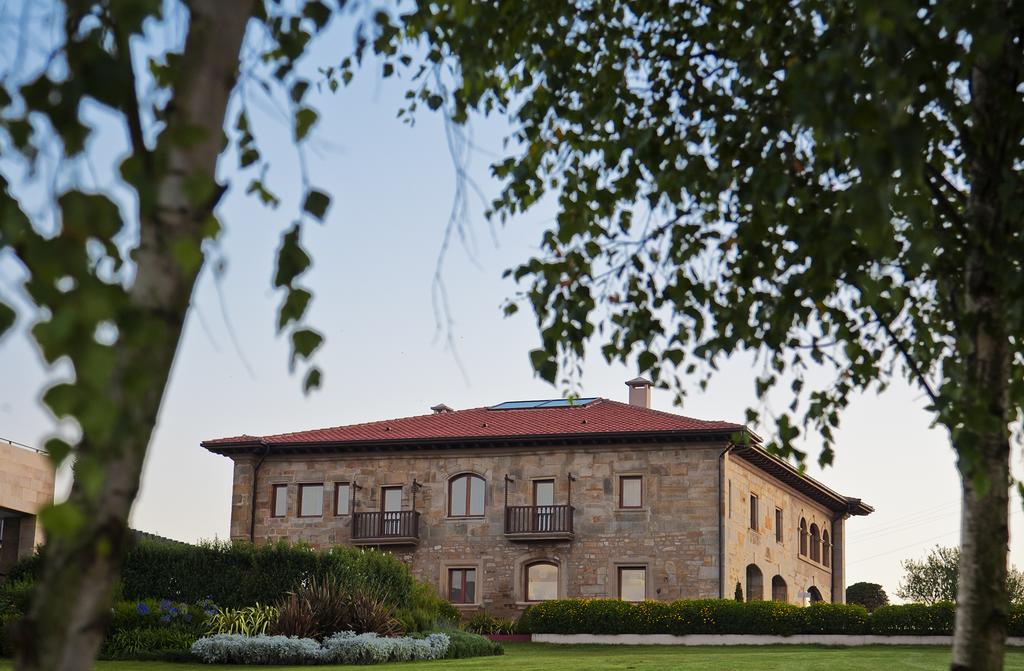
Antana comienza la segunda fase de rehabilitación del Hotel Palacio de Luces Relais&Châteaux.
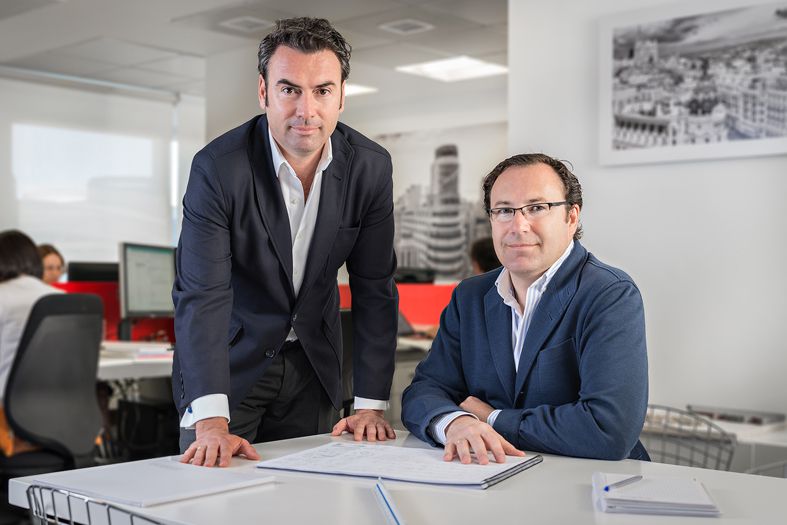